August 2008 Vol. 63 No. 8
General
Underground Installation Projects: Determining the Best Approach
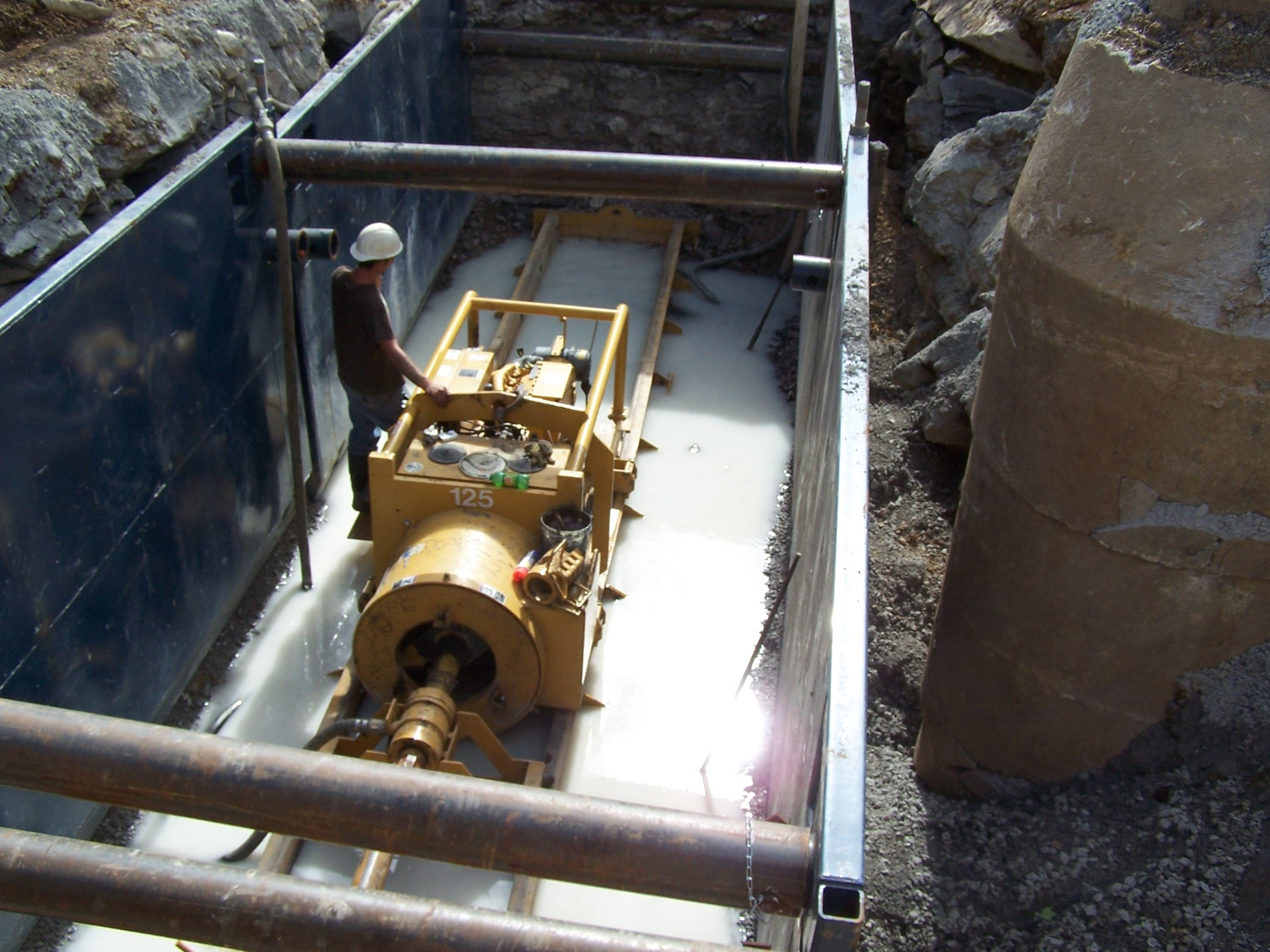
The first decision a contractor should make when preparing a bid for any trenchless job is to identify the application that will be most efficient to complete the project. Each trenchless method has its advantages and works better in specific situations. However, sometimes the most efficient approach may involve using a combination of applications, requiring equipment that contractors may not have in their fleet.
“Determining which trenchless method is the most appropriate is project specific,” says Eric Nicholson, director of global and key accounts with HammerHead. “If you have a project that requires the relocation of a line, then horizontal directional drilling (HDD) or pipe ramming may be a good option. If you are installing a new line on grade; auger boring, ramming or HDD are considerations. In the case of a water or sewer line rehabilitation project, bursting may be the best method.”
It’s important to look at each project individually and consider the space available, number of bores or bursts and their length to select the most effective trenchless method. Engineers should also involve the contractor in the planning phase and encourage their input as to which trenchless methods may be the most cost effective way to complete a project.
Right combination
Among the first things a contractor considers when bidding an underground installation project is which method will be most effective to complete the job. Since most underground projects are unique, contractors need to be careful to analyze each job in advance to develop a plan. Involving contractors as early as possible can minimize the owner’s potential liability.
“The process of determining which method is most appropriate varies based on a number of factors,” says Tom Davey with Cutting Edge Group, Lake George, N.Y. “Much will be dictated by access restrictions, ground conditions, project installation specifications and a combination of any or all of these variables. It’s not an exact science, however. When we estimate a job, we have to make some assumptions because you really never know what you’re going to encounter until you get into it. We usually have a pretty good idea of how we plan to approach it before going in, but the plan often changes along the way.”
Cutting Edge Group recently completed a job that involved replacing roughly 30,000 feet of water main at a campus in Wassaic, NY, using a variety of techniques. “We replaced a 980 foot run of 12 inch pipe using a HammerHead static bursting unit,” Davey says. “After that initial shot, it got a bit tricky with lots of turning points. So instead of digging entry and exit pits every 50 feet or so, we used a horizontal directional drill to install a new line offset from the original line. We used a combination of directional drilling and pipebursting – and a lot of engineering ingenuity.”
Trenchless methods uncovered
There are several different trenchless methods available to contractors and each has its specialty in the type of projects it can complete.
Bursting: Defined as the breaking of an existing pipe, and expanding the broken pipe shards into the surrounding soil while simultaneously pulling in the new line. Static or pneumatic pipe bursting has several distinct advantages. First, it’s easy on adjacent utilities because it follows the existing pipe path. Second, pipebursting can be used to increase a system’s capacity by upsizing the service line where cured in place and sliplining cannot. Third, since bursting is a trenchless process, minimal excavation is required, allowing contractors access to congested areas without hampering traffic flow or affecting expensive surface structures.
Projects best suited for pipebursting include the upsizing of existing service lines and replacement of aged pipelines, specifically sewer and water. Pipes suitable for pipebursting are typically made of brittle materials, such as vitrified clay, cast iron, plain concrete, asbestos or some plastics. Reinforced concrete pipe (PCP) can also be successfully replaced if it is not heavily reinforced or if it is substantially deteriorated. Ductile iron and steel pipes can also be burst using pipe slitters.
Pneumatic boring: Typically, this method is used to “punch” a hole under existing landscape and/or structures from a city connection directly to the home or business. Bores typically are 50 feet or less in length and the diameter ranges from 1.25 to eight inches. With only two small operating pits, boring with small diameter pneumatic tools minimizes above ground disturbance to existing landscapes, reduces cost and the amount of time necessary to complete the connection.
Ramming: Pipe ramming is a trenchless method for installing steel pipes and casing under roads, highways, rail beds and other structures. Pipe ramming tools have the ability to install steel casings up to 84 inches (and sometimes much more) in diameter, and are most useful for shallow installations where other trenchless methods could cause surface settlement or heaving. The majority of installations are horizontal, although the method can be used in vertical applications. One of the most common uses is to install casings for sensitive utilities and replace damaged culverts under roads and railroad tracks.
Pipe ramming tools can also be used to assist in HDD projects. To help overcome hydro lock situations, the hammer can be attached to the product during the pullback. The percussive action keeps the pipe moving and helps prevent high levels of pullback stress. This process can also be used to help free immobilized product.
Auger boring: Auger boring uses a rotating cutting head to bore a horizontal hole inside a casing. As the cutting head cuts through the ground, the resulting spoil is moved by the flighted auger out of the casing and the steel casing is jacked into place. Auger boring is ideal for boring in rock, cobble and unstable soil.
Horizontal directional drilling (HDD): Directional drilling is used for installing infrastructure, such as telecommunications, electric, water, sewer, gas, oil and product pipelines up to 60 inches in diameter. It is used for crossing waterways, roadways, shore approaches, congested areas, environmentally sensitive areas and areas where other methods are not practical or more expensive. HDD provides for reduced traffic disruption, lower cost, deeper and/or longer installation, no access pit, shorter completion times, directional capabilities and environmental safety. This method has extensive use in urban areas for developing subsurface utilities as it helps in avoiding extensive open cut trenches.
Combining methods
According to Dave Gasmovic, president and CEO of McLaughlin in Greenville, SC, a project may take more than one trenchless method for the job to be cost effective.
For example, portions of a sewer installation project may be suitable for directional drilling while an auger boring machine might be more suitable for a segment that requires a 400 foot grade shot.
“We encourage engineers not to tie contractors into one specific method,” says Gasmovic. “Tap into the contractor’s expertise to select the most cost effective method to complete the project.”
Jason Clark, owner and president of Iowa Trenchless in Panora, IA, recently used a pneumatic hammer and auger boring machine to upgrade a storm water system near Rockville, MN. The project called for installing 100 feet of 60 inch and 80 feet of 30 inch storm water lines under a Burlington Northern Railroad track. The only problem? Rocks. And lots of them.
The ground below the railway bed was mainly cobble and coarse wet sand. Boring or pipe jacking were not options due to the high risk of a hole opening caving in or collapsing due to the unstable ground conditions. But the resourceful Clark, after some thought and planning, figured he could use a pipe rammer to complete the project with some modifications to the plan.
“In these types of ground conditions, rammed pipe can swallow the material whole, including large rocks and cobble, keeping the pipe outside diameter to a minimum and saving cost on the job,” Clark says. “The material is not removed until after the casing is installed, reducing the risk of creating voids.”
The project required that the pipe be placed more than six feet underground with the two drainage lines installed at a 45 degree angle horizontally under the railroad bed – all while trains continued to pass on the tracks above.
Iowa Trenchless rented a 24 inch pneumatic pipe rammer from HammerHead to install the heavy wall steel pipe. When the full length of pipe was installed, the crew used an auger boring machine to remove the soil, cobble and sand that had accumulated inside the 60 inch and 30 inch pipes.
“I don’t think anyone knew what they were getting into at the time,” Clark says. “There was just no way to bore this project. But with some flexibility and ingenuity we were able to complete it successfully.”
Gasmovic has also worked with contractors who have used a directional drill to bore a pilot hole and then modify a boring machine to tie into the pilot stem. They then use the pilot hole as a guide to install a large diameter pipe with an auger.
Dilemma
For some contractors, using more than one trenchless method presents challenges. Most adversely affected is the smaller, independent operator who must prioritize equipment purchases based on the type of services they offer and perform most often. Many don’t own the equipment needed to perform all of the various approaches. Access to employees with the skills and knowledge to operate the machines specifically designed to perform varied applications also presents a dilemma.
“It can be very challenging for contractors to combine trenchless technologies on a project,” says Nicholson. “Contractors may lack the scale and the cost to mobilize multiple technologies and crews can be costly. A contractor needs to determine if the primary trenchless technology they use can be incorporated into the rest of the project. Using one method also reduces the engineering and permit requirements as well.”
Contractors who don’t own equipment have options. Rental and leasing programs abound; and many equipment manufacturers and dealers provide operator training and on site support.
“We want all of our customers to be able to compete on a level playing field,” says Ed Savage, trenchless segment manager for Vermeer. “Most of our dealers offer rental, lease and rent to own programs that allow all our customers, regardless of size or assets, access to equipment that allows them to compete for jobs they would not pursue otherwise. This has been good for the industry in general.”
“We leased a HammerHead unit for a project to burst heavy wall castings,” Davey says. “They sent out a guy who had been a contractor for nine years and could talk in layman’s terms to our guys in the field. He really knew what he was doing and knew all the tricks. Our guys were so confident after he left that we ended up buying the machine.”
“As technology and equipment innovations evolved, so have we,” Davey says. “Appropriately, the name of our company, Cutting Edge Group, is basic to the idea that we try to stay ahead of the curve and keep a broad information base that allows us to understand all the technology that’s out there. We’re really not afraid to jump into something, even if it means taking a hit on one job. It just needs to make economic sense when you look at the big picture.”
Vermeer Corp., (888) 837-6337, www.vermeer.com
Hammerhead (Earth Tool Corp.), (800) 331-6653, www.hammerheadmole.com
McLaughlin, (800) 435-9340, www.mightymole.com
Comments