April 2010 Vol. 65 No. 4
Features
Slide Rail Systems Offer Cost-Effective Trench Safety Option
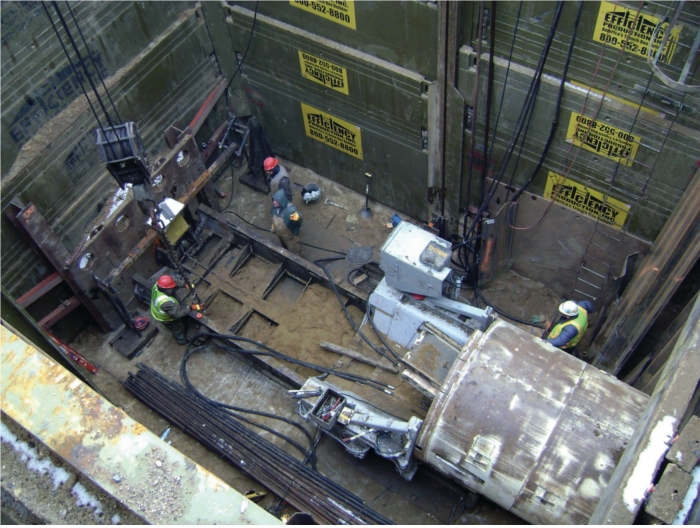
For excavation projects requiring manned entry, shielding and shoring trench walls is a major cost. Material and labor prices escalate as excavations cover more area and become deeper.
On many large projects — especially long runs of large-diameter pipe installation — slide rail systems have become the preferred method of preventing the collapse of trench walls. Proponents say that in most cases, slide rails can be installed faster and more economically than conventional methods.
A slide rail system is a component shoring system comprised of steel panels similar to trench shield side walls and vertical steel posts. It is installed as the trench or pit is excavated by sliding the panels into integrated rails on the posts — either double or triple rails depending on needed depth — then pushing the panels and posts incrementally down to grade as the pit is dug.
Modular slide rail systems may be used in a variety of configurations without cutting or welding. They do not require interior walers or beams which provides more working space in the excavation. Slide rail manufacturers say the systems can reduce shoring costs from 30 to 60 percent compared to conventional methods.
Representatives of three leading slide rail manufacturers recently commented to Underground Construction on the technology and the advantages it offers.
Efficiency Production, James McRay, director of marketing and media: “Slide rails have become a very popular alternative to applications that would require tight sheeting and are most effectively used in very encumbered areas where access to all four sides of an excavation is not possible. Because slide rails are comprised of component pieces, the entire system can be installed with access to only one or two sides. In many cases, traditional trench shields and shoring is just unfeasible, either due to the restrictions of excavation site, or the limitations of the excavator and other equipment. In those instances slide rails may be the only option. This is certainly true for very deep excavations, or when it is necessary to shore all four sides of an excavation.
“There are differences among the slide rail systems available today. The biggest is in applications that require a cross brace or spreader system and tend to vary widely between the manufacturers. Efficiency Production’s system of cross brace support utilizes parallel beams that pin in place standard trench box spreader pipes.
“We consider our ClearSpan slide rail system superior in several ways. First, it leaves the entire excavation completely unencumbered by any cross braces throughout the entire installation or removal process. The system has shored excavation more than 50-by-50-feet wide and more than 30-feet deep without cross braces.
“Next, our slide rail system has an open-face inside rail. When the inside, deeper panels are installed in the posts, the open face rails on the post allows some ‘slack’ in the panels which helps prevent the system from binding when installed; and makes it easier to remove the deep-set panels which always sustain the greatest force or pressure behind the panel.
“Finally, our team of slide rail experts has installed more than 200 slide rail systems in every conceivable configuration, and in the trickiest site conditions.
“On a recent project in Indiana, Efficiency’s engineers custom designed a slide rail system for an excavation to install a drop-assembly structure for a 72-inch pipe storm sewer outfall into a river. The pit was in a highly-congested area with one side approximately three-to-four feet from a structure. A two-bay, four-sided configuration was used with ClearSpan waler I beams to provide an unobstructed opening of more than 28 feet.”
Pro-Tec Equipment, Tommy Marciniak, marketing: “We have seen a continued increase in the use of the systems and the number of contractors willing to try it. Of course, each manufacturer wants to be able to separate itself from the others, and there are differences in some components, but for the most part, all the manufacturers slide rail systems will achieve the same goals; it is just a manner of how they are achieved that sets different systems apart.
“The Pro-Tec Equipment slide rail system is ideal for large clear-span operations such as installing large, cast-in place structures, single and multiple fuel tanks, for job sites sensitive to vibrations and jobs that have tight quarters. It is extremely versatile and can be made into a 2-, 3- or 4-sided system that can go to depths of 32 feet.
“The Pro-Tec P.I.T. Boss panel installation tool dramatically increases panel installation speeds, as well as reducing damage to the excavator bucket and slide rail panels.
“New for 2010, Pro-Tec has developed a four-way post that allows the system to do 90-degree turns.
“We believe the most important feature Pro-Tec equipment offers is service. We provide CAD drawings of systems, site-specific engineering if needed, and factory installers when necessary to ensure that the system gets put in place and removed in the safest, fastest most economical way possible.
“Recent projects of interest include shoring a 30-by-35-foot, 24-foot deep excavation adjacent to a pond. Were it not for the slide rail system’s ability to enable excavation and spoil removal from the bottom up, there would have been no way to complete the project other than tight sheeting which would have increased costs two to three times.
“For an excavation 15-by-20 feet and 20-feet deep to remove a section of damaged pipe and manhole, slide rails reduced time to complete the project by two to four days, compared to conventional shields or tight sheeting.”
Speed Shore, Steve Schulz, national sales manager: “As do other shoring and shielding products, slide rail systems have specific applications such as when a project requires there be little or no ground movement outside the excavation. As acceptance increases, slide rail systems are being used more frequently instead of driven sheeting or beam and plate systems. Benefits of slide rail systems include ease of installation and removal with much less vibration, more accommodating for backfill lifts and, in most cases, smaller excavator or equipment can be used.
“Differences in systems available are mostly in linear applications, the maximum width that can be obtained with pipe clearance and different levels of workmanship and materials.
“Speed Shore slide rails have always been built for tough service and have evolved to incorporate features built into the rails and panels that provide long service life.
“Interesting recent projects in Louisiana have utilized the Speed Shore linear system to widths exceeding 30 feet with the ability to assemble parallel struts at the excavation, rather than having to assemble rails and struts together and then having to move them to the excavation.”
FOR MORE INFO:
Efficiency Production, Inc., (800) 552-8800, www.epi-shields.com
Speed Shore Corporation, (800) 231-6662, www.speedshore.com
PRO-TEC Equipment, (800) 292-1225, www.pro-tecequipment.com
Comments