April 2010 Vol. 65 No. 4
Rehabilitation
April Rehab News: Insituform Awarded $6.7M Contracts, Proactive Sliplining and Robots to Rescue of Aging Pipes
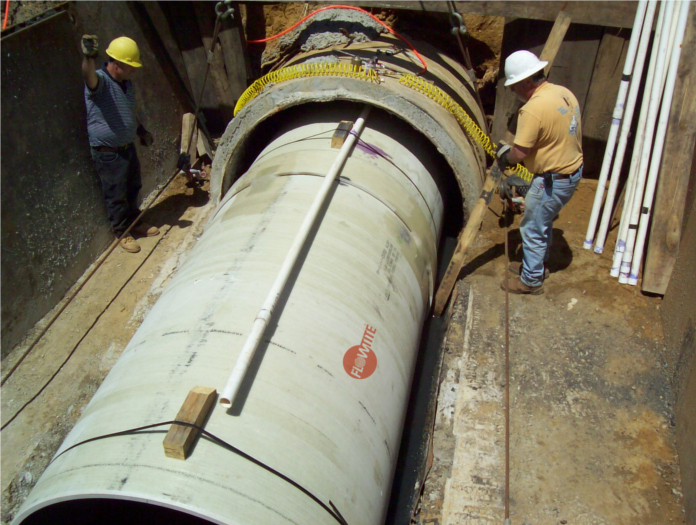
Insituform awarded domestic, international contracts
Slipline fits in proactive approach
Robots to help repair aging water pipes
Insituform awarded domestic, international contracts
Insituform Technologies Inc. has been awarded $6.7 million in sewer pipe rehabilitation work for Pell City, AL, which has used a grant from the American Recovery and Reinvestment Act of 2009 to award the largest CIPP project in Pell City’s history to Insituform. Under this contract, Insituform will rehabilitate approximately 115,000 feet of sewer pipelines in residential and rural areas. This contract also marks the first time Insituform has worked with Pell City.
Insituform cured-in-place pipe (CIPP) will be used to eliminate inflow and infiltration on the 25-year old small- to medium-diameter sanitary sewers. Work on this project was expected to begin in February 2010 and take approximately one year to complete.
On the international front, Insituform’s Singapore subsidiary, Insitu Envirotech has been awarded four contracts totaling $18.5 million. Under the contracts, Insituform will perform work for the Public Utility Board (PUB), Singapore’s national water agency, and rehabilitate approximately 50 miles of sewer pipeline though the use of the Insituform CIPP process. Insituform also announced it has received an additional $1.4 million in orders to supply CIPP tube to third parties in Singapore.
In 2009, PUB, Singapore’s publicly-owned water utility, began work on a multi-year $295 million rehabilitation program. This rehabilitation program is expected to be completed in 2014 and will upgrade over 700 miles of public sewers and 30 miles of pumping mains. PUB serves a population of over 4.5 million Singaporeans. These contracts are part of PUB’s ongoing rehabilitation program.
The iPlus Infusion system for small-diameter wastewater pipelines and the iPlus Composite system for medium- to large-diameter wastewater pipelines will be used for the first time in Singapore on this project. These next-generation CIPP solutions provide PUB with an environmentally beneficial solution. Insituform plans to utilize its air invert steam cure (AISC) technology to complete this project, which will reduce water and energy usage on the job site by approximately 95 percent.
Insituform expects this project will create 45 new positions including laborers, field management and administrative personnel in Singapore. In addition, locally-owned subcontractors will be used to complete work on this project, which was expected to begin in March 2010 and be completed by December 2011.
Slipline fits in proactive approach
By acting before a problem became an emergency, planners in Hamilton Township, NJ, took a proactive approach to rehabilitating an existing sanitary sewer pipeline showing signs of deterioration in its crown. The 72-inch diameter reinforced concrete influent pipeline passed underneath Interstate I-195 and the Township needed to keep the line in use during the necessary construction work. Since there was no practical way to bypass the flow, sliplining the pipe under flow conditions was the chosen installation method.
The slipline utilized in the Hamilton Township Treatment Plant Headworks Rehab
Project, Final Phase, consisted of 330 linear feet of 66-inch diameter Flowtite fiberglass reinforced plastic pipe with inherent wall-to-wall non-corrosive properties. Pipes were delivered in 10-foot lengths for this gravity application. The pipes were unique in that each section was fitted with four 4-inch by 8-inch laminated skids, spaced 12 inches apart, in order to assist the contractor during installation. Flowtite is manufactured by US Composite Pipe South, Zachary, LA.
“These skids helped with the alignment of the bell and spigot during the joint connection process,” stated Richard Palmer, P.E., tunneling manager for Northeast Remsco Construction Inc., of Farmingdale, NJ. “The skids also kept the coupling from scraping along the bottom of the host pipe during installation, avoiding potential damage to the coupling.
“The preparation and cleaning of the host pipe was probably the most challenging part of the project. After providing mechanical ventilation, we used a combination of jet/vac cleaning and manned entry/clean-by-hand methods to extract the debris and verify that we had adequately cleaned the entire length of the host pipe prior to inserting the Flowtite pipe.”
He continued that all were pleased with the performance of the Flowtite pipe and that delivery of the 33 10-foot pieces, along with a 66 inch by 36 inch Flowtite tee base fitting, was timely and according to schedule.
Robots to help repair aging water pipes
An engineering team at the University of California, Irvine are building a robot that can travel along water pipes and repair them from the inside. If this project is successful, a commercialized robotic system could give the U.S. a lead in the growing world market for water infrastructure technology
The American Society of Civil Engineers which rates the quality of city infrastructure, including water works, estimates 6 billion gallons of clean drinking water disappears each day, mostly due to old, leaky pipes and mains.
In order to address the problem, a UCI engineering research team is building a robot that can travel along water pipes and repair them from the inside. The team is also working with Fibrwrap Construction Inc. and Fyfe Company LLC, two companies that specialize in making repair materials and applying them to city infrastructure.
The robot is expected to save cities time and money by accessing broken and leaking pipes faster, easier and with fewer resources than traditional methods.
The repair robot could easily be inserted into water systems, travel along them until it finds a break or weak point, and then apply a patch made of tough reinforcement material along the inside of the pipe. Essentially, the robot would create a new fiber pipe inside the old damaged one.
The obstacles for this project involve creating a way for the robot to accurately identify flaws in pipes that have unpredictable shapes and uneven surfaces. Another problem is how to apply the reinforcement material.
The research team is integrating an advanced sensor system into the robot that can measure contact pressure against the sides of the pipe and activate the repair process where appropriate.
The robots can be built for various types and sizes of pipes and repair them 11 times faster than human crews, according to a team representative.
Comments