June 2010 Vol. 65 No. 6
Features
New EPA Regulations Will Require Machine Reconfiguring, Add Cost
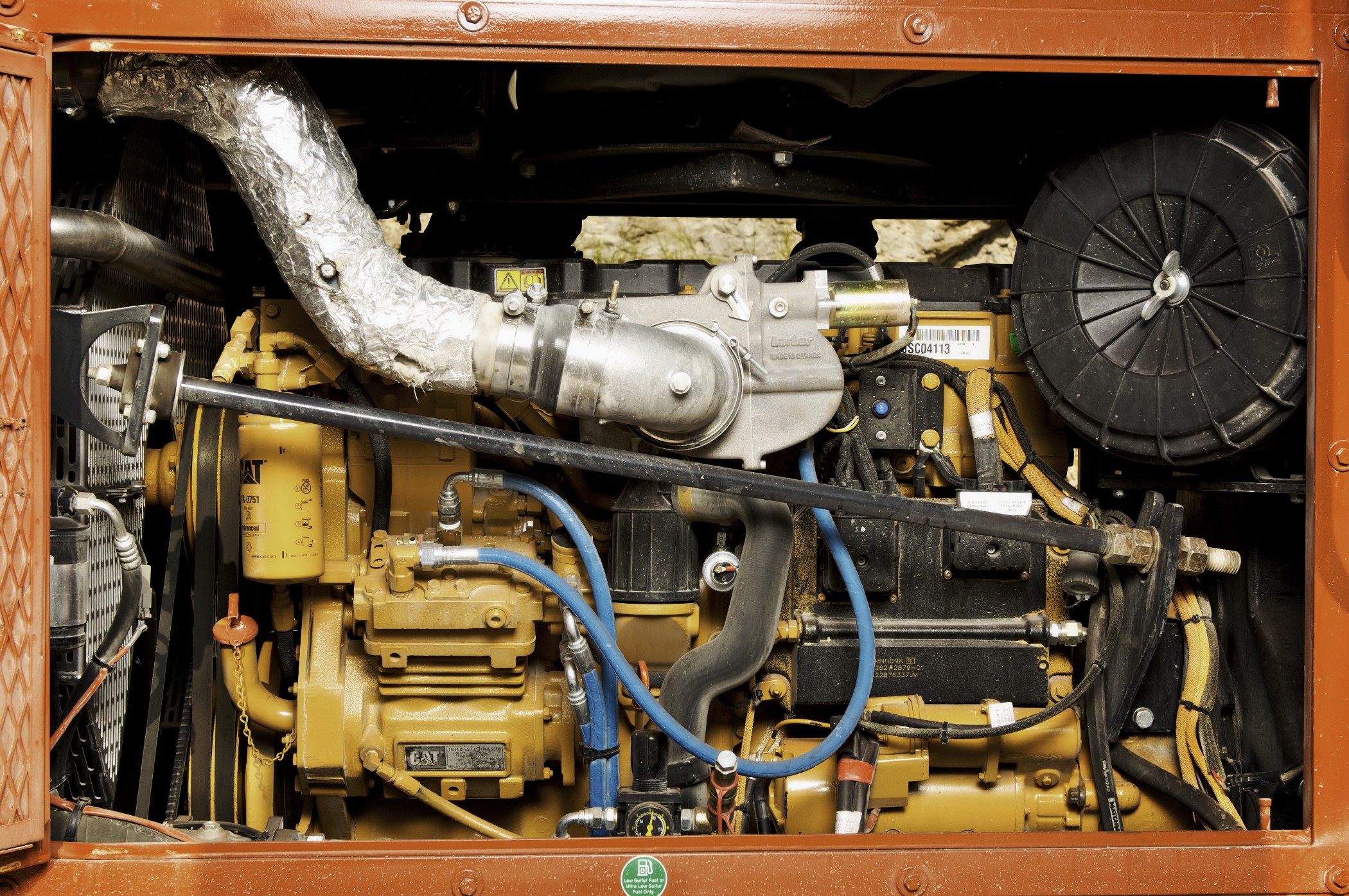
In less than six months, the U.S. Environmental Protection Agency (EPA) Interim Tier 4 emission standards will go into effect for many types of off-road diesel powered equipment used in underground construction, and equipment owners and operators are devoting increasing attention to the changes they will bring.
On Jan. 1, 2011, engines between 74 and 175 horsepower installed in off-road machines must use “cleaner” diesel fuel and oil and will be equipped with filters requiring maintenance previously not needed on older engines. Ultimately the requirements will increase the cost of new machinery equipped with Tier 4-compliant engines.
Final Tier 4 regulations will begin to be implemented in 2014. They will maintain the high reduction of particulate matter required in intermediate Tier 4, but will mandate a substantial increase in the reduction of nitrogen oxide (NOx) emissions. Engines 175 to 750 horsepower will be affected on Jan. 1, 2014. Those 75 less than 174 horsepower will be affected on Oct. 1, 2014. These are engine build dates.
There are several technologies to accomplish this, but the consensus of engine and OEM manufacturers is that whatever methods are used will add to the cost of new equipment The stricter final Tier standards will bring to off-road equipment requirements already in effect for over-the-road trucks, so experiences with trucks could be an indication of what to expect with off-road machinery.
Representatives of two engine manufacturers and two major underground equipment suppliers recently shared their insight as to what kind of impacts the underground industry might expect when final Tier 4 becomes effective.
John Deere Power Systems, Doug Laudick, manager of product planning: “The purpose of Final Tier 4 emissions regulations is to further reduce NOx. Final Tier 4 regulations will maintain levels of particulate matter (PM) and require an additional 80 percent reduction in NOx compared to Interim tier 4/Stage III B.
“All engines will be affected. The method used to achieve Final Tier 4 standards will depend on the engine power level. John Deere is continuously developing and testing the technologies it will adopt to achieve Final Tier 4/Stage IV emissions regulations.
“For engines 130 kW (174 hp) and greater beginning in January 2014, proven technologies such as cooled EGR and VGT will likely be the foundation for meeting those regulations. However, we are constantly evaluating emerging technologies for their effectiveness and for their ability to provide reliable and durable products in off-highway applications. As with engine configurations that meet previous emissions tiers, we’ll continue to tailor our Final Tier 4 engine solutions to fit the variety of off-highway applications, while not increasing the emissions compliance burden on our customers.
“It is anticipated that technologies similar to those used in on-highway engines will trickle down into off-highway products. However, one of the biggest challenges is the rate at which these technologies — originally developed for on-highway use — must be adapted for off-highway use. The time between adoption of a new technology for on-highway engines and its use in off-highway applications has continued to decrease. Off-highway equipment often works in harsher and more varied environments. Additional development time is required to make on-highway technologies suitable for off-highway applications. Ensuring the robustness of these technologies for off-highway use will continue to be a challenge through Final Tier 4/Stage IV.”
Case Construction Equipment, Richard Heisey, director, engine installation competence center: “Case has developed for interim Tier 4 standards a solution that relies on two technologies: cooled exhaust gas recirculation (CEGR) and selective catalytic reduction (SCR). Our priority is to provide our customers with cost-efficiency and performance, and we see advantages to both technologies, depending on engine size and load, as well as application demands. We are fortunate in having access to the tremendous resources and experience in CEGR and SCR technologies of our strategic partners which include Fiat Powertrain Technologies, a pioneer in low emission systems.
“For Final Tier 4, we will continue to work with our partners on developing the solution that will guarantee our customers the cost-efficiency and performance they expect of our equipment. The introduction of SCR technology as early as 2011 gives us a competitive advantage, because we have already invested in R&D that will be invaluable in helping us to achieve Final Tier 4 requirements. Having similar technology now allows us to keep our research investments focused on developing the next generation of construction equipment that will set new standards in cost-efficiency, productivity and performance.
“In developing our SCR technology solutions we benefited from Fiat Powertrain Technologies’ consolidated experience from on-road Tier 2 and Tier 3 applications developed for engines in more than 100,000 trucks and commercial vehicles sold since 2006. This extremely valuable resource, coupled with the tremendous construction equipment design expertise of our global R&D teams, has enabled us to develop SCR solutions specifically optimized for the load cycles of off-road equipment.”
Charles Machine Works, David Campbell, priority project manager: “Equipment owners need to know that equipment will be more expensive — my estimate is a 5 percent MSRP increase for equipment larger than 174 horsepower. For equipment between 75 and 174 horsepower, the increase may be larger. They will be expensive to operate. An additional consumable fluid will likely be needed. Also, additional steps may be needed to prepare for long-term equipment storage.
“Equipment manufacturers will need to modify equipment to accommodate Final Tier 4 engines. The SCR module is expected to be somewhat larger than a conventional muffler. These modules will be similar in size to the DPFs that will be added starting in 2011. An additional tank for diesel exhaust fluid (DEF), which SCR requires, will be needed. DEF consumption is expected to be 2 to 5 percent of fuel consumption. As a bare minimum, the DEF tank should be 5 percent as large as the fuel tank. Depending on the OEM’s chosen DEF refill strategy, the tank could be much larger. Electronic components to monitor and control the SCR performance plus a pump to control the DEF usage rate will be integral parts of the system. Finally, the DEF tank will need heating components to thaw the fluid when temperatures are below 15 degrees Fahrenheit.
“The SCR systems that are expected in 2014 should be very similar to those introduced on model year 2010 trucks. There will likely be some differences between on-road and off-road applications, but I expect those to be subtle.
“I am not aware of any particular routine maintenance issues with SCR. There is at least one intermittent issue related to machine storage. DEF is a 32.5 percent aqueous urea solution, meaning it is 67.5 percent water and 32.5 percent urea. When a machine is unused for an extended period, the water can evaporate, leaving a solution that has a higher than desired concentration of urea. In the worst case, all the water evaporates leaving urea crystals in the tank. The DEF tank should probably be drained if a user expects to park a machine for an extended period.”
Vermeer Corporation, Ed Savage, trenchless segment manager: “Many equipment owners operate globally today, making it important to understand the different certification requirements by region and equipping their fleet appropriately is important. Fuel standard will also play an increasingly significant role region by region. For example, only low-sulfur diesel is compatible with Tier 4-certified engines, but is not available in all areas. Equipment owners should stay in tune with project-based emission certification requirements that may restrict them from bidding on a project based on their fleet.
“We expect the Tier 4 engine and after-treatment packages to be considerably larger in size. Our challenge as an OEM is redesigning around the physically larger engines while retaining the existing footprint of similarly powered, non-Tier 4 equipment.
“We expect final Tier 4 engines to cause an increase in the cost of equipment. The percentage increase will vary by horsepower class.”
FOR MORE INFORMATION:
John Deere Power Systems, (800) 533-6446, www.deere.com/en_US/rg/index.html
Case Construction, (262) 636-6772, www.casece.com
Charles Machine Works, (800) 654-6481, www.ditchwitch.com
Vermeer Corp., (888) 837-6337, www.vermeer.com
Comments