August 2011, Vol. 66 No. 8
Features
Soil Stabilization With Grout
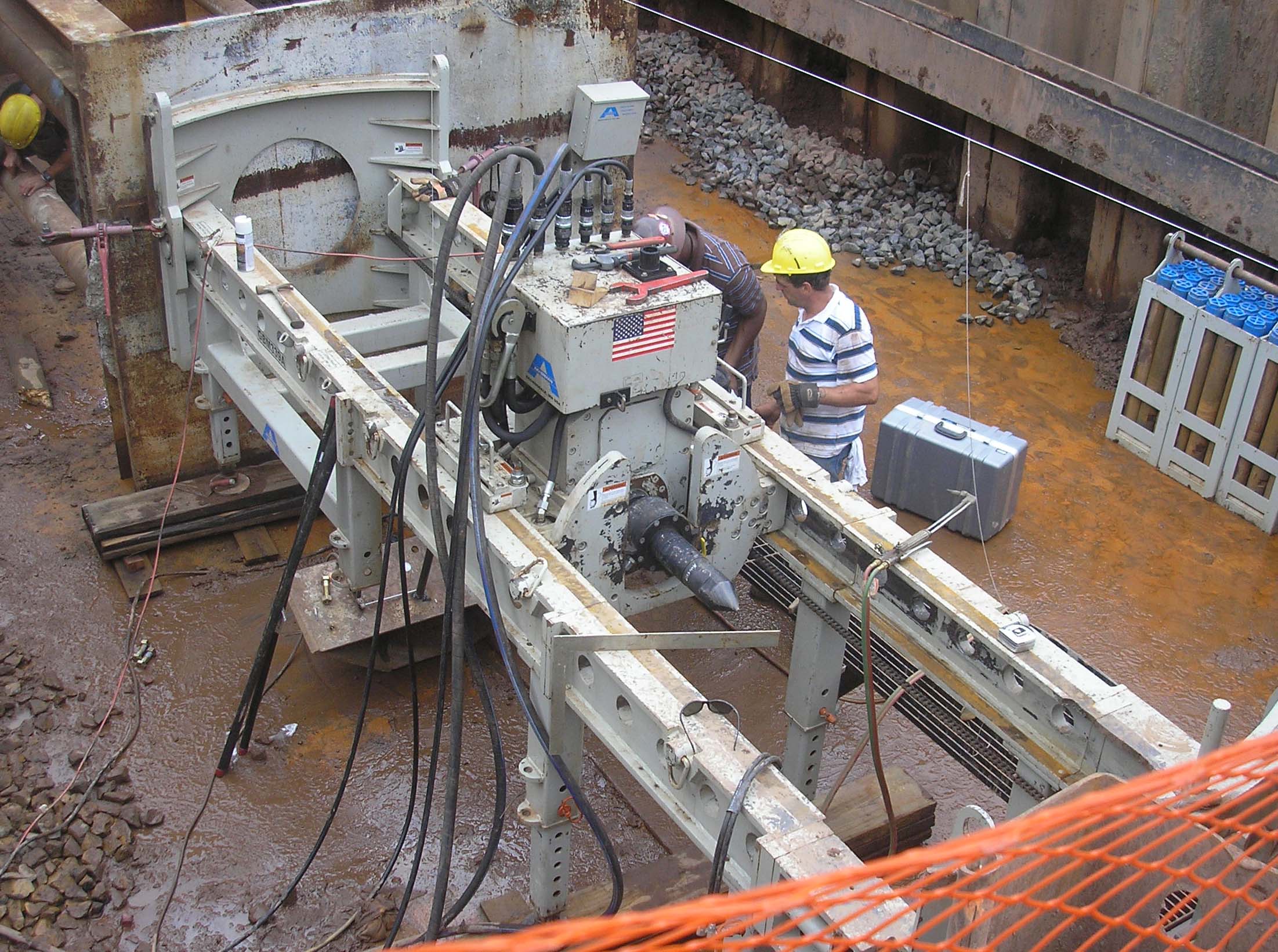
Stabilization of soil to ensure the ground will support foundations and the weight of buildings, highways, bridges and other improvements is a critical element in construction projects.
Soil or ground stabilization also comes into play for underground utility construction projects. The two basic stabilization methods — mechanic and additive – are applicable to utility as well as civil and commercial projects. The type of stabilization process used depends on the level of stabilization required and conditions on the project site.
Ground stabilization in excavation and tunneling often is called “support of excavation,” said Guy Dickes, president, Constellation Group LLC.
“Because ground cannot stand up by itself and tends to collapse, trench boxes are used in cut and cover projects and sheet piling is used for shafts and excavations,” Dickes said. “Grouting is used to control water and stiffen the surrounding soils.”
The Constellation Group recently provided ground stabilization consulting services to Northeast Remsco for a project to replace a sewer outfall for the Somerset Raritan Valley (New Jersey) Sewer Authority.
A railroad line crosses the route of the pipeline, requiring a 201-foot-long, 108-inch diameter liner-plate tunnel under three railroad tracks. Cut and cover was not viable as the railroad tracks were in daily operation. No interference with railroad operations would be allowed.
Northeast Remsco performed the tunnel operation. Once the liner plate tunnel was complete and grouted, NRC then poured a pad to slipline the 72-inch PCCP carrier pipe inside the newly constructed 108-inch LP tunnel. The annular space was then pumped/filled with a low density cellular concrete fill by NRC. The invert of 108-inch diameter steel pipe was set approximately 13-25 feet below the surface. The top of the pipe was approximately four to 16 feet below the railroad tracks and ground.
The 25-foot-deep launch pit was set up on the north side of the railroad tracks with the receiving pit at the south side.
Soil stabilization
To protect the tracks on the surface, soil stabilization was required. A previous attempt by another contractor had failed, and Dickes said the railroad was extremely concerned that the installation of the tunnel not causes settling of soil which would have halted vital rail traffic.
The contract permitted a maximum of 0.5 settlement of the railroad tracks, said Dickes. Anything more would cause the project to be shut down.
“For this project,” said Dickes, “ground stabilization prior to tunneling was the only option. Ground stabilization grouting in advance of tunneling is a proven technique and has been used for many years. The primary goal was to control water and prevent subsidence of the active railroad tracks passing over the planned tunnel, and grouting was used to prevent uncontrolled soil erosion into the tunnel bore.”
Dickes said Constellation Group provided consulting services so that Northeast Remsco could self-perform the grouting operation. Working closely with NER Project Manager Giovanni Scotto, these services included overall grout submittals, operations planning, equipment and material selection and operation, quality control and full-time grouting supervision. Extensive surveying was done prior to, during and after grouting and tunneling operations.
The project engineering team selected sodium silicate grout for the project.
“Some of its advantages,” Dickes explained, “are low cost compared to other chemical grouts; its ability to strengthen the soil; low environmental impact; and very low viscosity enabling it to be pumped long distances and to permeate into fine sands and silts.
“Sodium silicate is a highly predictable and proven grout that can be controlled as to strength and set time. It produces excellent results in sandy/gravelly soils. It is readily available in large quantities from numerous sources and also environmentally friendly.”
Dickes said prior to tunneling it was necessary to install 11 horizontally located sleeve port pipes (SPPs), also called tube-a-manchettes (TAMs). The pipes were installed approximately 18-22 inches outside the planned tunnel alignment and parallel to it.
Equipment
An Akkerman Model 339A guided boring machine (GBM) was used to advance a 4½-inch pilot hole. After exiting the opposite pit, the SPP was attached and pulled back to the launch pit. As the SPP was installed, a casing grout was pumped to fill the annular space left by the drill. These 11 pipes were installed radially along the tunnel alignment from the 7 o’clock position to the 5 o’clock position. This annular grout is designed to fracture easily, but fill the bore hole so sodium silicate grout does not follow the SPP bore, but goes into the ground.
The upper sleeve port pipes were constructed of 1½-inch PVC, the lower ones SPPs were steel. Port spacing was every 15 inches.
“Grouting commenced in an alternate pipe (staggered) sequence, and from top to bottom,” Dickes said. “Specifications required three grouting passes. Each pass on each pipe required about 160 individual episodes — that’s 11 pipes, 160 ports and three passes for nearly 5,280 grout episodes. The first pass required 30 gallons per port, the second pass seven gallons, and the third pass, between three and 10 gallons. In total, nearly 80,000 gallons of sodium silicate were pumped.”
The grout plant operation included three 3,000 gallon storage tanks, two sets of dual grout pumps, two transfer pumps and two mixing pumps.
Dickes said crews faced two major challenges.
The first occurred shortly before operations began when equipment planned for the project became unavailable. Working together, team members assembled necessary equipment and parts.
“The second challenge was changing ground conditions for installing the SPPs,” Dickes said. “Upper ground conditions were sand/gravel making SPP installation easy. The lower ground conditions included larger stone and required the change to steel sleeve port pipes.”
Grouting operations required eight weeks. Northeast Remsco installed the 72-inch PCCP outflow pipe in late fall 2010, and tied it into manholes located at each end of the tunnel.
When completed, grouting reduced water infiltration into the tunnel from 60 to 80 gallons per minute (gpm) to less than 5 gpm.
There was no appreciable settlement of the railroad track, meeting the less than one-half-inch specification.
The Constellation Group is a construction consulting business and has worked on numerous major projects in the United States, Canada and Spain, providing expertise in helping contractors self-perform specialty tasks, such as on this project. Dickes has 30 years experience in the construction field.
Established in 1956, the Somerset Raritan Valley Sewerage Authority is located in Somerset County, NJ, and serves seven communities: Branchburg, Bridgewater, Hillsborough, Manville, Raritan, Somerville and Warren. The authority operates a 21.3 mgd secondary wastewater treatment system with sludge managed with a fluidized bed incinerator.
In addition to processing wastewater, the authority accepts graywater, septage and sludge.
FOR MORE INFO:
Constellation Group LLC, (410) 484 0672; www.cgllc.us
Akkerman Inc., (800) 533-0386, www.akkerman.com
Comments